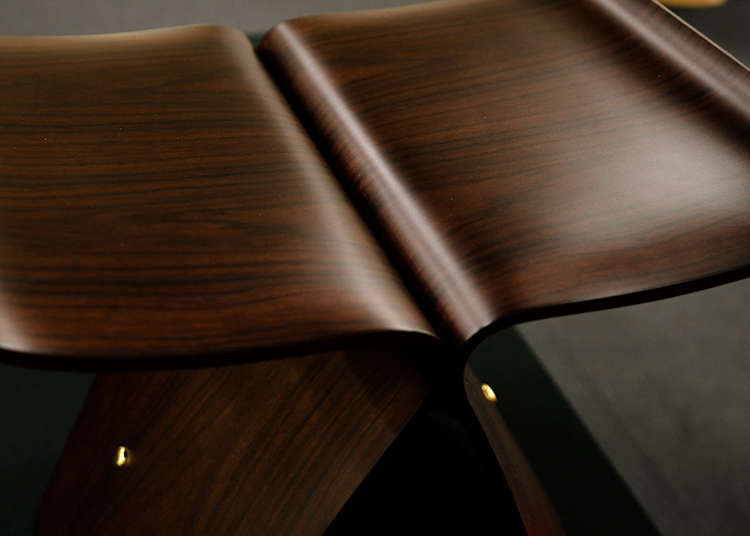
Why Are Japanese Wood Furniture Makers, Known for 'Design Masterpieces,' Admired Around the World?
- Written by: LIVE JAPAN Editor
Japan’s rich forests are a source for its acclaimed furniture. Here, many manufacturers harness the wood’s natural texture, and the craftsmanship behind these high-quality designs has gained global recognition.
Known for its innovative woodworking products such as the Butterfly Stool, we visited Tendo Co., Ltd. to discover the essence of the skills of Japan’s leading woodworking furniture craftspeople.
*This article includes advertising content.
Why Japanese Woodworking Furniture Remains Unbreakable and Beautiful
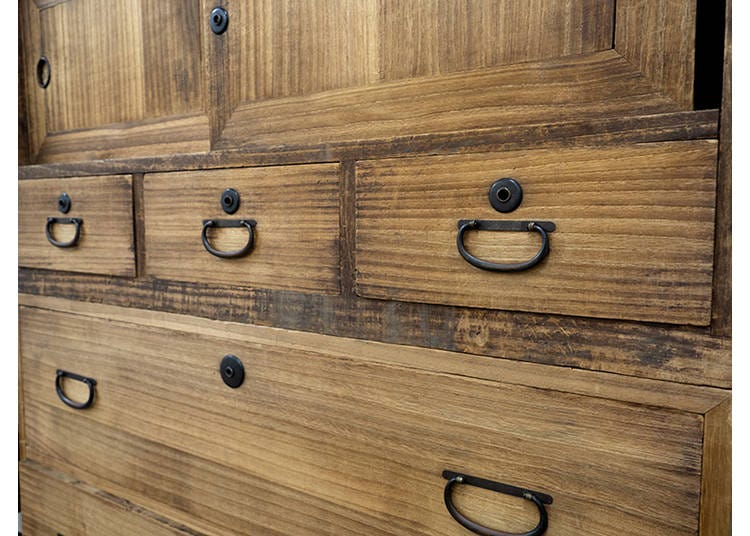
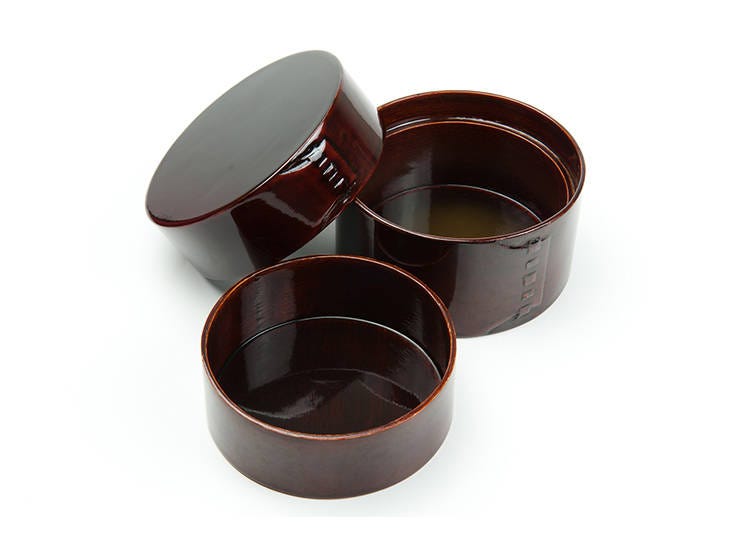
Japan has been rich in forest resources since the B.C. era, and woodworking products have long been a part of the lives of Japanese people. Delicate processing techniques such as “sashimono,” which involves joining pieces of wood together without the use of metal fasteners to make furniture, and “magemono,” involving bending wood into a circular shape to make tea sets and lunch boxes, dates back more than 1,000 years.
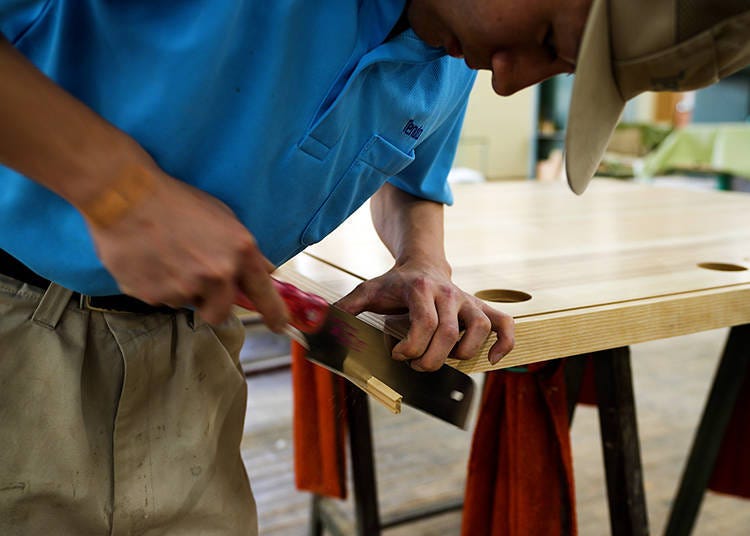
With the growing demand to make furniture for the imperial family and samurai lords, furniture craftspeople specializing in making wooden furniture such as chests and “zataku (low tables)” began to appear in various parts of the country.
The honor and dedication of making such items for those of high society led to the evolution of techniques for making wooden furniture that were sturdy, durable, and aesthetically pleasing. Pursuing a quality that would satisfy the imperial family and samurai lords, Japanese woodworking techniques have evolved into a world-class craft.
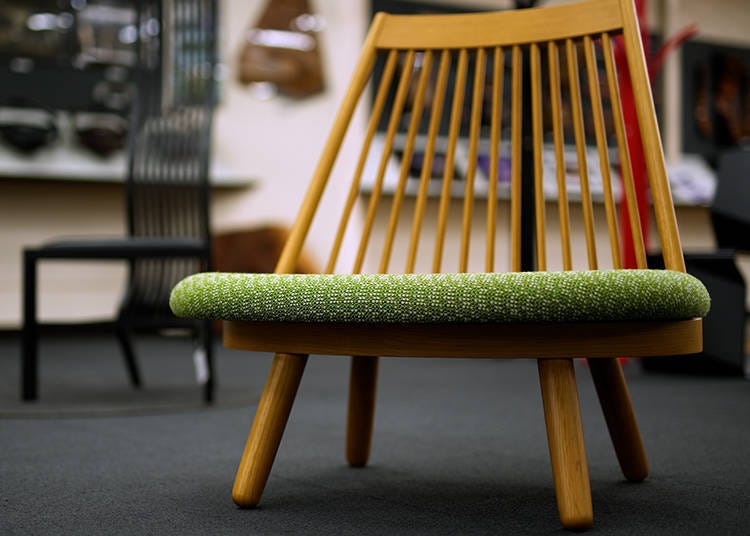
By the Meiji Period (1868–1912), Western culture began to be introduced in Japan, followed by the Taisho Period (1912–1926), when the government took the initiative in promoting the westernization of the lives of the common people. Driven in part by the popularity of Bunka Jutaku houses with Western-style parlor rooms, furniture manufacturing of tables, chairs, and other furniture suited to Western lifestyles began to flourish more than 100 years ago.
Butterfly Stool Craftsmanship Brings World Recognition of Japan Quality
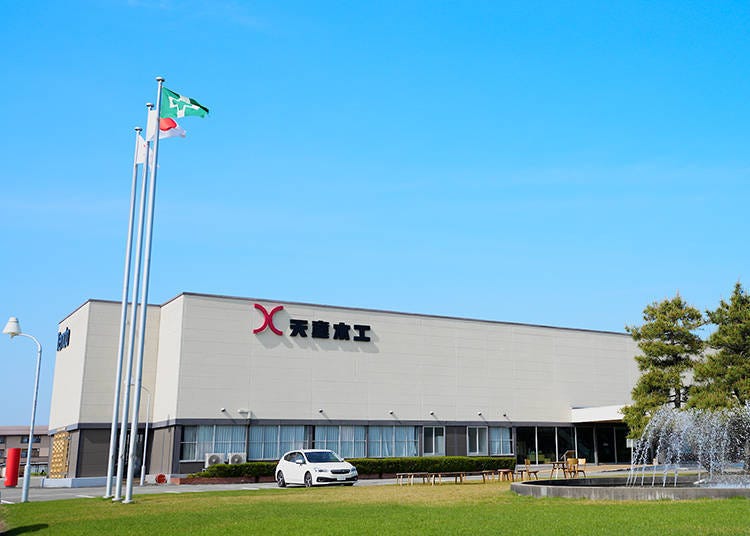
Nestled in a nature-rich basin near the Ou Mountains, Tendo Mokko in Tendo City, Yamagata Prefecture, emerged from a collective of carpenters, woodworkers, and sashimono artisans.
These experts, hailing from a region with a rich history in woodworking, joined forces to form an industrial association. This collaboration marked the beginning of their journey into mass-producing molded plywood furniture, rapidly elevating Tendo Mokko to the ranks of Japan’s top furniture manufacturers.
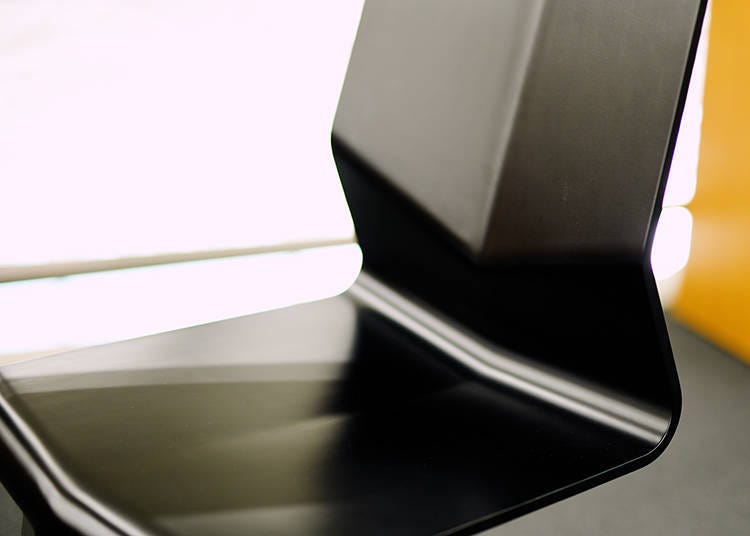
Molded plywood processing is a technique for creating various shapes by placing thin sheets of wood about one millimeter thick one on top of the other so that their grain lines intersect, then placing them in a pressure press and gluing them together by applying high-frequency heat.
The most distinctive feature of this technique is that it allows for a wide range of designs to be realized. Flexible, strong, lightweight, and easy to handle, it adds a touch of charm to daily life. The molded plywood technology that offers all the advantages of furniture has attracted many architects and designers and has produced world-class masterpieces in collaboration with Tendo Mokko.
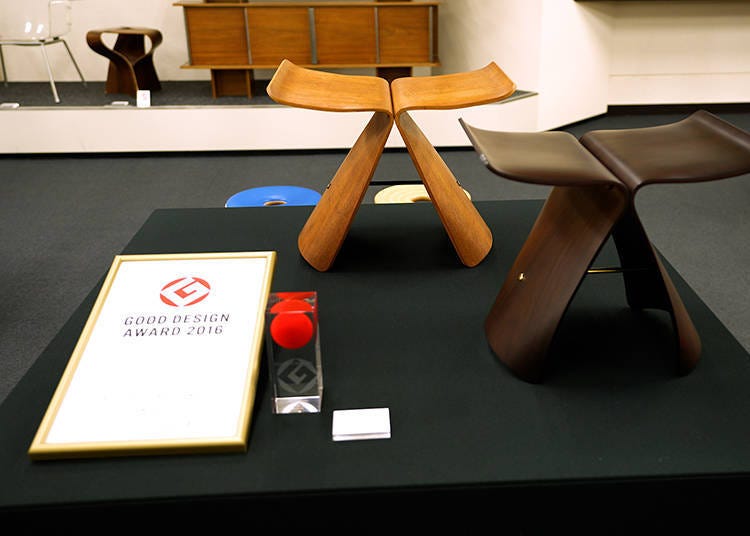
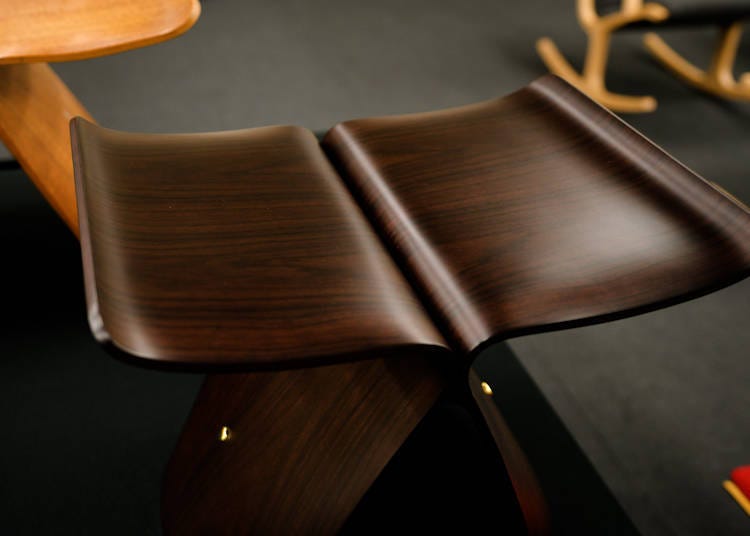
A representative example is Sori Yanagi’s Butterfly Stool, created in 1956. While the design is simple, consisting of symmetrically joined pieces of molded plywood of the same shape, the perfect curves of the stool, like a butterfly spreading its wings, remain beautifully lean and perfectly formed, and even half a century after its birth, it is still a signature product of Tendo Mokko. Collected by the Louvre Museum and the Museum of Modern Art in New York, it is also referred to as a “masterpiece of design history.”
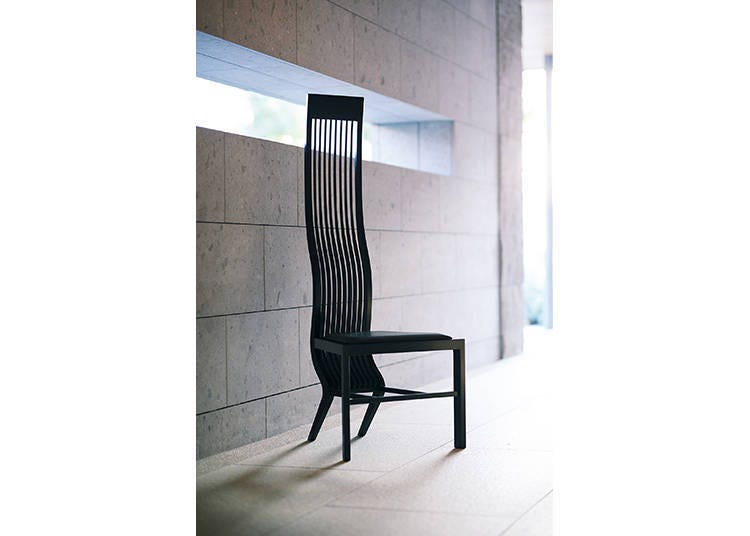
Another masterpiece is the Monroe Chair, created by world-renowned architect Arata Isozaki, which, as its name suggests, was inspired by Marilyn Monroe’s body lines to recreate the undulating curves in the form of woodwork.
Hearing Every Creak - The Obsession of Japanese Furniture Craftsmen
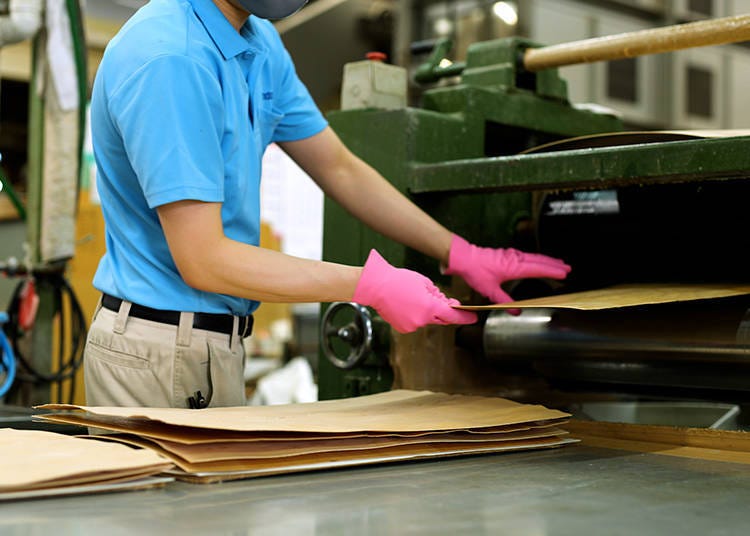
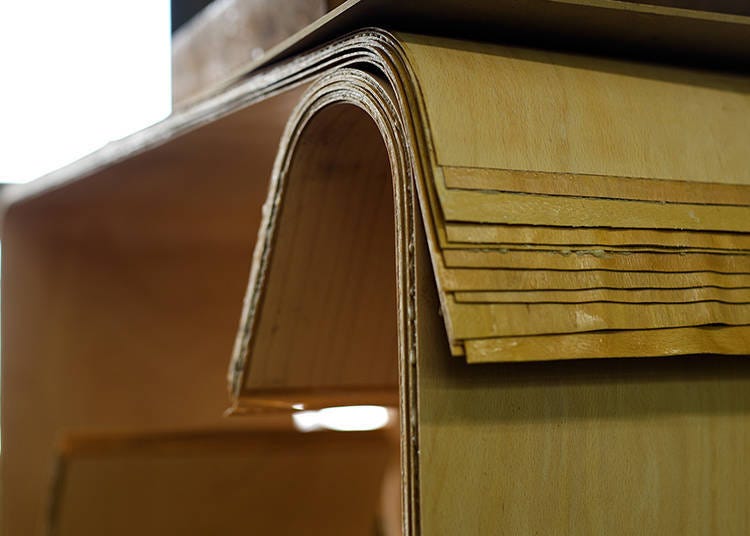
In fact, molded plywood processing is not an unusual technique in countries that produce a lot of wooden furniture. However, “Japanese furniture craftspeople have persistence,” says Mr. Imada of Tendo Mokko. All craftspeople take great care and diligence to ensure that not even a single defective piece is produced and that the boards are firmly fixed in place.
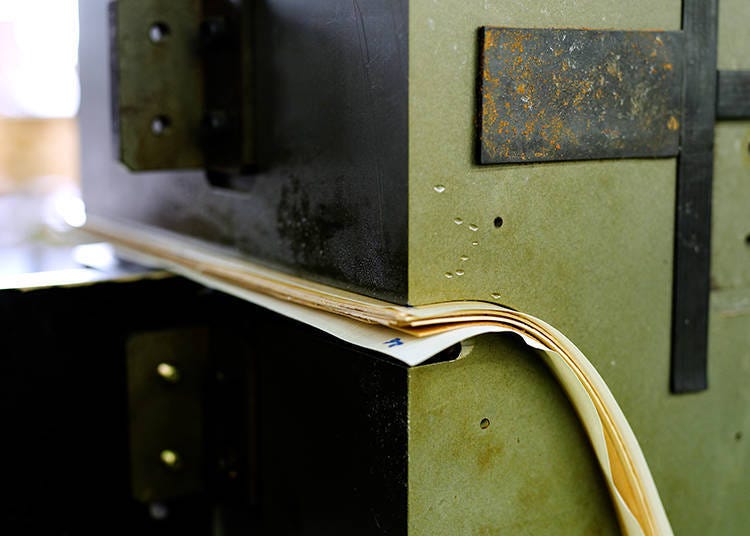
During the shaping process using a high-frequency press, there is a faint creaking sound, which the craftsperson listens to as they apply pressure, gradually adjusting the pressure as they go. Depending on the furniture design, the time and direction of the pressure will vary, and it is left up to the craftsperson to determine.
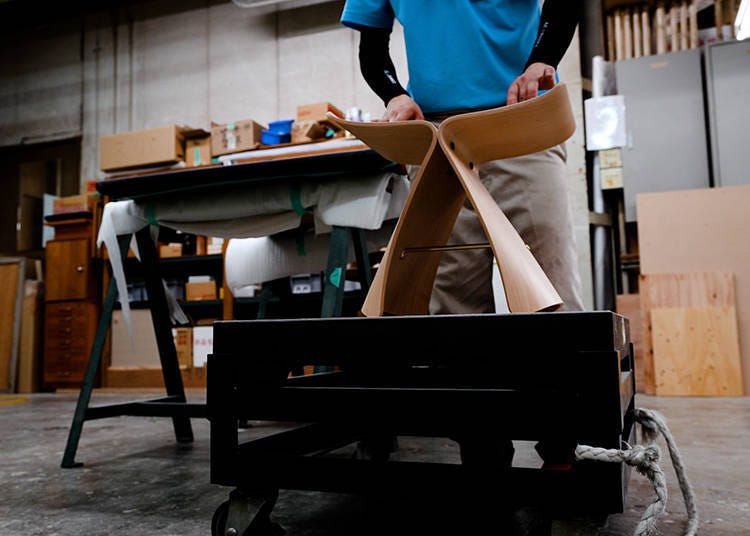
The butterfly stool is also made by layering sheets of wood one on top of another so that the grain of the wood intersects, increasing strength and creating a design as delicate as a butterfly’s wings. The grain pattern, which appears symmetrical when assembled, is selected from the sliced boards to be closer to one another. The persistence in maximizing the molded plywood technology to create a stronger and more beautiful finish can be considered unique to Japan.
Globally Acclaimed - Japanese Woodworking Techniques Bring Coniferous Trees to Life
Nestled among forests, Japan produces not only woodworking products that showcase the skills of its craftspeople but also furniture made from flexible coniferous wood, which is generally not utilized to the same extent as other materials.
Founded in 1920, Hida Sangyo Co., Ltd., a long-established furniture manufacturer, developed Sugi lumber suitable for furniture making in cooperation with the local forestry cooperative in Gifu Prefecture.
Since coniferous wood is softer than hardwood, Sugi wood is carefully pressure-pressed to ensure its strength. Together with designers from Japan and abroad, the company has been promoting the appeal of furniture made of coniferous wood worldwide, including at the Salone Internazionale del Mobile (Milan International Furniture Fair), one of the largest furniture exhibitions in the world. Another comprehensive furniture manufacturer, Karimoku Furniture, Inc., founded in 1947, has also created a collection of furniture named MAS, which is made of Japanese softwoods such as Hinoki. With innovations in the structure and the use of hardwood for the core material, the original beauty of softwood can be fully brought to life while ensuring strength.
Meanwhile, Tendo Mokko pioneered the Roll Press Wood, a technique for applying softwood to molded plywood. Earning the Prime Minister’s Prize of the Monodzukuri Nippon Grand Award in 2015, this technology has created furniture with aesthetic curves that have never been seen in softwood furniture before.
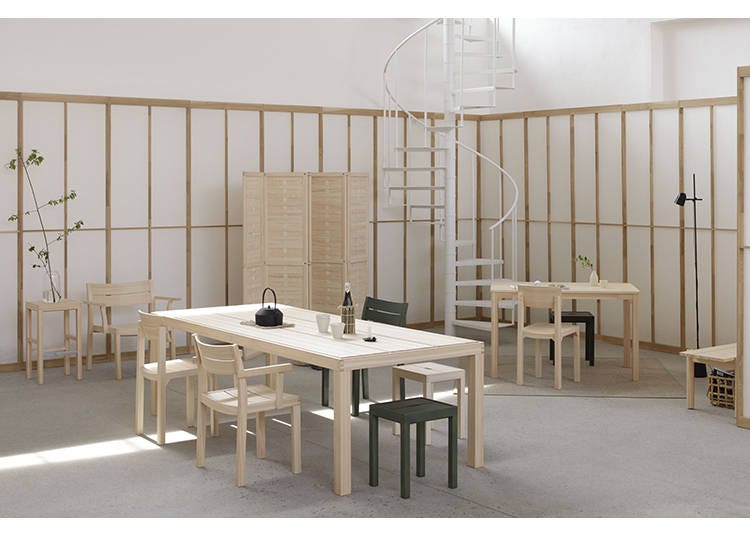
Globally, it’s rare to see softwood used in furniture and buildings. Achieving a quality that's both robust and durable enough for outdoor use is a testament to the relentless dedication of furniture manufacturers and forestry cooperatives. Their goal is to utilize resources efficiently while preserving nature’s bounty.
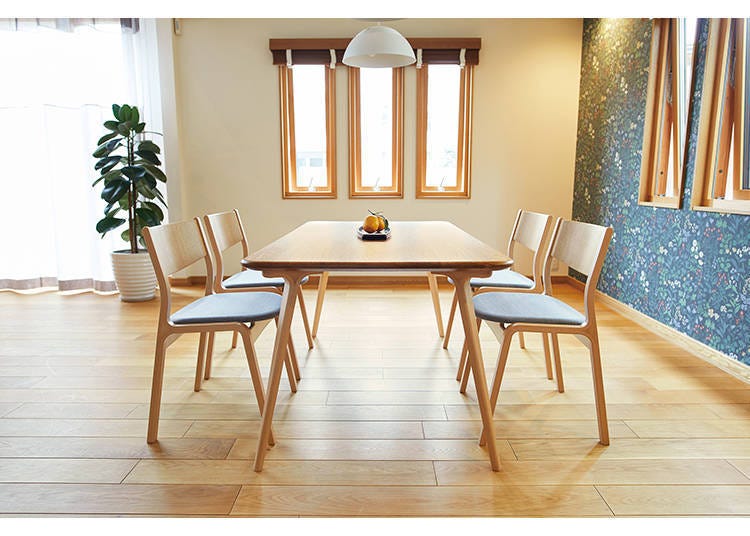
Drawing supple curves and bringing out the finest qualities of wood, Japanese woodworking furniture offers a serene interior decor. Come and incorporate Japanese wooden furniture that brings a sense of warmth and comfort into your life.
- Area
- Category
*Prices and options mentioned are subject to change.
*Unless stated otherwise, all prices include tax.
-
Ad
Why Fukushima is the Next Big Food Destination in Japan The Foodie Paradise Only 90 Minutes from Tokyo
-
Ad
Meet GU, UNIQLO’s Stylish Sister Brand! Fashion-Forward Clothing in the Latest Colors (Featuring Exclusive Coupon)
-
Top 10 Places in Akita to See the Cherry Blossoms in 2025
by: Alexander Litz
-
Disney Meets Shinkansen: Two Themed Trains to Explore Japan's North and South in 2025
-
Dining in Yamagata: Must-Try Foods & Top Restaurants Near the Station
by: ShiroKu inc.
-
Shopping in Niigata: 9 Must-Buy Souvenirs & Local Sake to Take Home
by: ShiroKu inc.
-
Shopping in Akita: 11 Must-Buy Souvenirs & Where to Shop Near the Station and Airport
by: ShiroKu inc.
-
10 Aomori Souvenirs Recommend by An American Living in Aomori
-
What to Buy in Aomori? 11 Aomori Souvenirs Locals Actually Recommend
by: ShiroKu inc.
-
Tokyo to Sendai: Riding the Shinkansen to Japan's Stunning Spots
-
(Video) Walking Tour along Narita Omotesando - Quaint Historical Village near Narita Airport!
by: Victor Gonzalez
-
18 Travel Secrets of Aomori Japan: Guide for Sightseeing, Shopping, and More